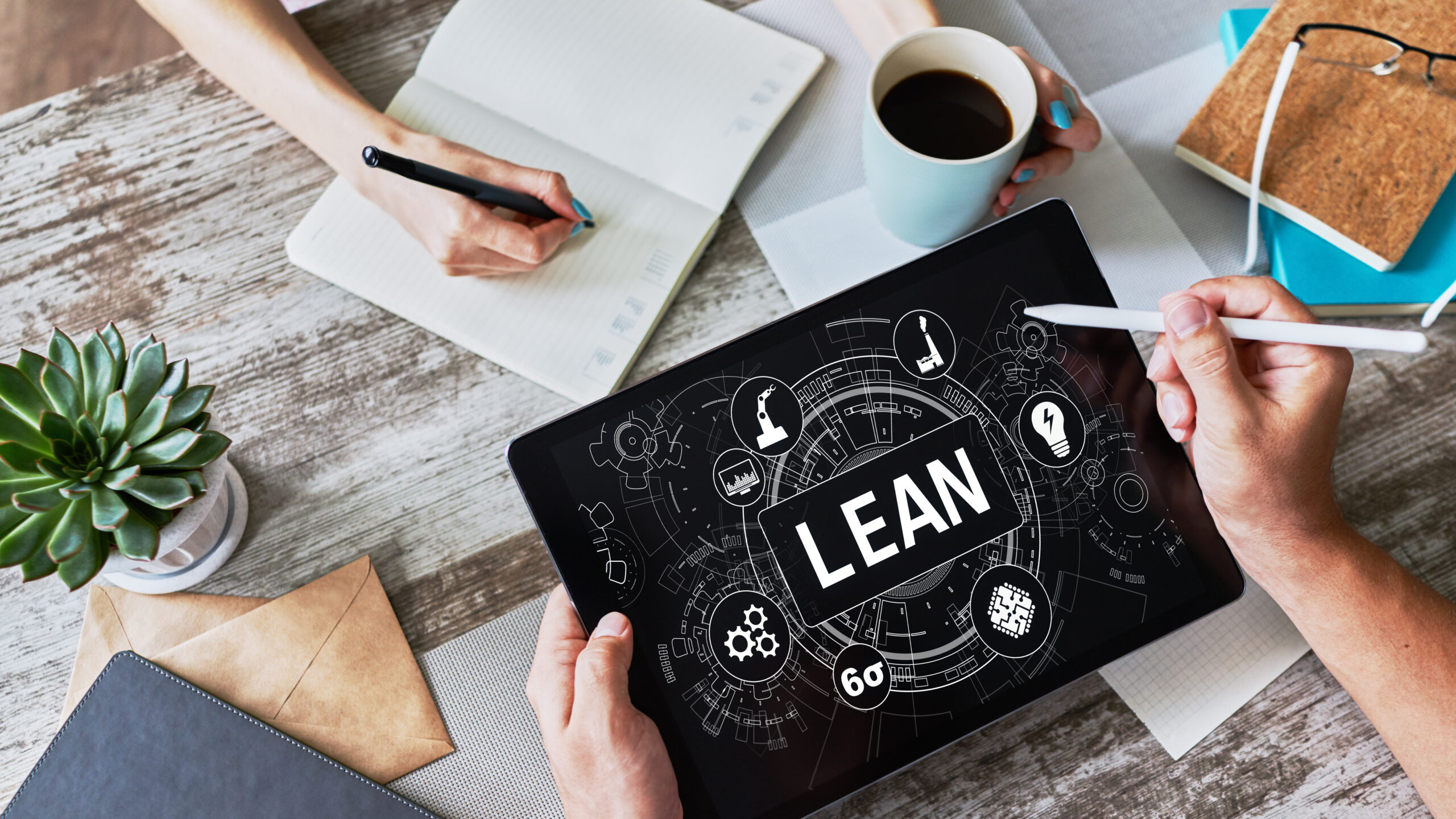
Exzellentes Lean Management: Auf dem Pfad zur Effizienzoptimierung und nachhaltigen Veränderung in der Organisation
Lean Management, ein Begriff, der in den letzten Jahrzehnten die Geschäftswelt revolutioniert hat, steht für eine Philosophie, die auf Effizienz, Verschwendungsbeseitigung und kontinuierlicher Verbesserung abzielt. Doch was bedeutet wirkliche Lean Management? Jenseits von oberflächlichen Anpassungen und kurzfristigen Effekten birgt die wahre Essenz des Lean Managements eine tiefgehende Veränderung in der Denkweise und Arbeitsweise von Unternehmen.
Um die Wurzeln des Lean Managements zu verstehen, muss man einen Blick auf die Entstehung in der Automobilindustrie werfen. Toyota, oft als Vorreiter des Lean Managements betrachtet, entwickelte das System, um Verschwendung zu minimieren und eine schlanke Produktion zu erreichen. Die Grundprinzipien, wie sie in den ursprünglichen Toyota-Produktionssystemen festgelegt wurden, bilden die Basis für wirkliche Lean Management-Praktiken.
Grundprinzipien des wirklichen Lean Managements:
- Verschwendungsbeseitigung: Wirkliches Lean Management zielt darauf ab, alle Formen von Verschwendung zu eliminieren. Dabei geht es nicht nur um materielle Ressourcen, sondern auch um Zeit und menschliche Potenziale. Durch eine gründliche Analyse aller Prozesse identifiziert und reduziert Lean Management Verschwendung auf allen Ebenen.
- Kontinuierliche Verbesserung (Kaizen): Ein entscheidendes Merkmal des wirklichen Lean Managements ist der Fokus auf kontinuierliche Verbesserung. Dieser Prozess ist nicht nur auf die Produktion beschränkt, sondern erstreckt sich auf alle Bereiche eines Unternehmens. Mitarbeiter werden ermutigt, ständig nach Möglichkeiten zur Optimierung ihrer Arbeit zu suchen.
- Pull-Prinzip: Im Gegensatz zum traditionellen Push-System, bei dem Produkte auf Vorrat produziert werden, setzt das Pull-Prinzip des Lean Managements auf die Produktion basierend auf tatsächlicher Kundennachfrage. Dies minimiert Überproduktion und reduziert Lagerbestände.
- Einbeziehung aller Mitarbeiter: Wirkliches Lean Management erfordert die aktive Einbeziehung aller Mitarbeiter auf allen Ebenen. Jeder wird ermutigt, Probleme zu identifizieren und innovative Lösungen vorzuschlagen. Teamarbeit und Kommunikation sind Schlüsselaspekte, um die Ideenflüsse zu fördern.
Herausforderungen bei der Umsetzung:
Die Implementierung von wirklichem Lean Management ist keine einfache Aufgabe. Unternehmen stoßen oft auf Widerstände gegen Veränderungen und müssen eine Kultur der Offenheit und Zusammenarbeit kultivieren. Zudem erfordert die Umstellung Zeit und Ressourcen, da sie die Neugestaltung von Prozessen und Schulungen der Mitarbeiter einschließt.
Wirkliches Lean Management geht über oberflächliche Maßnahmen hinaus und erfordert eine grundlegende Umgestaltung der Denkweise und Arbeitsweise von Unternehmen. Die Integration der Grundprinzipien, insbesondere Verschwendungsbeseitigung und kontinuierliche Verbesserung, führt zu einer nachhaltigen Veränderung und verbessert nicht nur die Effizienz, sondern auch die Agilität und Wettbewerbsfähigkeit von Unternehmen in einer sich ständig wandelnden Geschäftswelt.
Was ist der Unterschied zur japanischen Lean Philosophie und dem amerikanischen Lean Management?
Die Begriffe „Lean Philosophie“ und „Lean Management“ werden oft synonym verwendet, aber es gibt Unterschiede in der Herangehensweise, insbesondere zwischen der ursprünglichen japanischen Lean-Philosophie und den darauf aufbauenden amerikanischen Lean-Management-Praktiken. Hier sind einige Schlüsselunterschiede:
1. Kultureller Kontext:
- Japanische Lean-Philosophie: Die Wurzeln des Lean Managements liegen in Japan, insbesondere im Toyota-Produktionssystem. Die japanische Kultur prägte die Entstehung von Lean und betonte Aspekte wie Respekt vor Menschen, Teamarbeit und ständige Verbesserung (Kaizen).
- Amerikanisches Lean Management: Als Lean Management in den USA eingeführt wurde, wurden die Prinzipien an die kulturellen Gegebenheiten und Unternehmensstrukturen angepasst. Der Fokus lag oft stärker auf Effizienz, Kostensenkung und schneller Umsetzung.
2. Umfang und Anwendung:
- Japanische Lean-Philosophie: In Japan erstreckt sich Lean über den gesamten Lebenszyklus eines Produkts oder einer Dienstleistung. Es umfasst nicht nur die Produktion, sondern auch Design, Lieferkettenmanagement und Kundendienst.
- Amerikanisches Lean Management: In den USA konzentriert sich Lean Management oft auf operative Prozesse, insbesondere auf die Produktion. Es wird häufig als ein Set von Tools und Methoden betrachtet, die darauf abzielen, Verschwendung zu reduzieren und Effizienz zu steigern.
3. Kulturelle Prinzipien:
- Japanische Lean-Philosophie: Respekt vor Menschen, Teamarbeit, langfristige Denkweise und kontinuierliche Verbesserung sind zentrale kulturelle Prinzipien der japanischen Lean-Philosophie.
- Amerikanisches Lean Management: In den USA kann der Fokus stärker auf individueller Leistung und kurzfristigen Ergebnissen liegen. Obwohl Prinzipien wie kontinuierliche Verbesserung übernommen werden, können kulturelle Unterschiede zu unterschiedlichen Interpretationen führen.
4. Flexibilität und Anpassung:
- Japanische Lean-Philosophie: Die japanische Lean-Philosophie betont Flexibilität und Anpassungsfähigkeit. Das System soll sich ständig verändern und verbessern, um sich neuen Herausforderungen anzupassen.
- Amerikanisches Lean Management: In den USA kann Lean Management mehr formalisiert sein und sich auf standardisierte Methoden konzentrieren. Dies kann zu einer gewissen Steifheit führen, wenn es darum geht, sich schnell an sich ändernde Umstände anzupassen.
Insgesamt sind die Unterschiede zwischen der japanischen Lean-Philosophie und dem amerikanischen Lean Management oft subtil und können stark von der individuellen Auslegung und Umsetzung abhängen. Viele Organisationen kombinieren Elemente beider Ansätze, um eine passende und wirksame Lean-Praxis zu entwickeln.
Vor- und Nachteile
Lean Management kann für Organisationen eine Reihe von Vor- und Nachteilen mit sich bringen, abhängig von der effektiven Implementierung und Anpassung an die spezifischen Gegebenheiten. Hier sind einige der wesentlichen Vor- und Nachteile:
Vorteile des Lean Managements:
- Effizienzsteigerung:
- Vorteil: Eine der zentralen Zielsetzungen von Lean Management ist die Verschwendungsbeseitigung. Dies führt zu effizienteren Prozessen, Reduzierung von Überproduktion und Optimierung von Ressourcennutzung.
- Kosteneinsparungen:
- Vorteil: Durch die Reduzierung von Verschwendung und die effizientere Nutzung von Ressourcen können Organisationen ihre Kosten senken, was zu einer verbesserten Wirtschaftlichkeit führt.
- Kundenzufriedenheit:
- Vorteil: Lean Management setzt einen starken Fokus auf die Erfüllung der Kundenanforderungen. Durch eine flexible Produktion und schnelle Reaktion auf Kundenbedürfnisse kann die Kundenzufriedenheit erhöht werden.
- Kontinuierliche Verbesserung:
- Vorteil: Die Implementierung von Lean Management fördert eine Kultur der kontinuierlichen Verbesserung (Kaizen), bei der Mitarbeiter aktiv dazu ermutigt werden, Prozesse ständig zu optimieren.
- Agilität:
- Vorteil: Lean Management ermöglicht Organisationen, agiler auf Veränderungen im Markt zu reagieren. Durch das Pull-Prinzip kann die Produktion flexibel an die tatsächliche Kundennachfrage angepasst werden.
Nachteile des Lean Managements:
- Initiale Kosten und Ressourcenbedarf:
- Nachteil: Die Einführung von Lean Management erfordert oft erhebliche Investitionen in Schulungen, Veränderungsmanagement und möglicherweise neue Technologien. Dies kann zu anfänglichen finanziellen Belastungen führen.
- Widerstand gegen Veränderung:
- Nachteil: Mitarbeiter und Führungskräfte könnten Widerstand gegen die Veränderungen zeigen, die mit der Umstellung auf Lean Management verbunden sind. Dies kann die Umsetzung erschweren und die Effizienz beeinträchtigen.
- Risiko von Überlastung:
- Nachteil: Eine zu starke Fokussierung auf Effizienz kann dazu führen, dass Mitarbeiter überlastet werden, was langfristig zu Stress, Burnout und sinkender Arbeitszufriedenheit führen kann.
- Komplexität der Umsetzung:
- Nachteil: Die Implementierung von Lean Management kann komplex sein und erfordert eine sorgfältige Planung und Koordination. Fehlende Erfahrung oder unzureichende Schulung können zu Herausforderungen führen.
- Fehlende Anpassung an verschiedene Branchen:
- Nachteil: Lean Management wurde ursprünglich in der Produktion entwickelt und kann möglicherweise nicht nahtlos auf alle Branchen übertragen werden. In einigen Dienstleistungssektoren oder kreativen Bereichen ist eine Anpassung erforderlich.
Insgesamt können die Vorteile von Lean Management die Nachteile überwiegen, wenn es sorgfältig und angepasst implementiert wird. Eine umfassende Analyse der spezifischen organisatorischen Anforderungen ist entscheidend, um die Wirksamkeit von Lean Management zu maximieren.
Mögliche Stolpersteine
Die Einführung von Lean Management kann auf verschiedene Herausforderungen und Stolpersteine stoßen. Hier sind einige häufige Schwierigkeiten, die Organisationen bei der Implementierung von Lean Management begegnen könnten:
- Widerstand gegen Veränderung:
- Mitarbeiter und Führungskräfte könnten sich gegen Veränderungen sträuben, insbesondere wenn Lean Management tiefgreifende Umstrukturierungen mit sich bringt. Ein Mangel an Verständnis oder Akzeptanz kann den Erfolg der Implementierung gefährden.
- Fehlende Führungsbeteiligung:
- Das Engagement und die aktive Beteiligung der Führungsebene sind entscheidend für den Erfolg von Lean Management. Wenn Führungskräfte nicht vollständig dahinterstehen oder nicht aktiv am Veränderungsprozess teilnehmen, wird es schwierig sein, die Organisation erfolgreich umzustrukturieren.
- Unklare Ziele und Strategien:
- Fehlende klare Ziele und Strategien für die Implementierung von Lean Management können zu Verwirrung und Frustration führen. Organisationen müssen genau definieren, was sie erreichen möchten und wie sie dies umsetzen wollen.
- Mangelnde Schulung und Ressourcen:
- Mitarbeiter benötigen Schulungen, um die Prinzipien des Lean Managements zu verstehen und umsetzen zu können. Ein Mangel an Schulungen und Ressourcen kann die Wirksamkeit der Implementierung beeinträchtigen.
- Fehlende Kommunikation:
- Eine klare Kommunikation über die Gründe für die Einführung von Lean Management, die Vorteile und den Prozess ist entscheidend. Mangelnde Kommunikation kann Unsicherheiten und Ängste hervorrufen.
- Starre Umsetzung ohne Anpassung:
- Die starre Umsetzung von Lean-Praktiken ohne Berücksichtigung der spezifischen Bedürfnisse und Strukturen einer Organisation kann zu Widerstand und Ineffizienz führen. Lean Management muss an die individuellen Gegebenheiten angepasst werden.
- Fehlende Langfristperspektive:
- Lean Management ist kein kurzfristiges Projekt, sondern erfordert eine langfristige Verpflichtung. Organisationen, die sich nur kurzfristig engagieren, könnten die langfristigen Vorteile des Lean Managements verpassen.
- Schwierigkeiten bei der Messung des Fortschritts:
- Es ist wichtig, klare Leistungsmetriken zu definieren, um den Fortschritt bei der Implementierung von Lean Management zu messen. Ohne geeignete Messinstrumente kann es schwierig sein, den Erfolg zu bewerten und Anpassungen vorzunehmen.
- Übermäßige Fokussierung auf Kostensenkung:
- Wenn Lean Management ausschließlich auf Kostensenkung ausgerichtet ist, kann dies zu kurzfristigen Maßnahmen führen, die die langfristige Effektivität der Organisation beeinträchtigen.
- Unzureichende Identifikation von Verschwendung:
- Eine genaue Identifikation von Verschwendung ist entscheidend für den Erfolg von Lean Management. Fehlende Analysefähigkeiten oder Ignorieren bestimmter Arten von Verschwendung können die Effektivität beeinträchtigen.
Um diese Stolpersteine zu überwinden, ist eine sorgfältige Planung, klare Kommunikation, Schulung der Mitarbeiter und eine ständige Bereitschaft zur Anpassung der Implementierungsstrategie erforderlich. Lean Management erfordert eine umfassende kulturelle Veränderung, die Zeit und Engagement erfordert.
Diese Phasen zur Einführung empfehlen Experten
Die Einführung von Lean Management erfolgt in der Regel durch mehrere Phasen, um einen strukturierten und erfolgreichen Übergang zu gewährleisten. Die genauen Schritte können je nach Organisation variieren, aber hier sind allgemeine Phasen, die von Experten empfohlen werden:
- Vorbereitung und Planung:
- In dieser Phase werden die Ziele für die Einführung von Lean Management definiert. Die Führungsebene sollte sich klar über die Vorteile im Klaren sein und einen umfassenden Plan entwickeln. Dies beinhaltet oft Schulungen für Mitarbeiter und Führungskräfte sowie die Festlegung von Zielen und Metriken zur Bewertung des Fortschritts.
- Schulung und Sensibilisierung:
- Schulungen sind entscheidend, um sicherzustellen, dass Mitarbeiter auf allen Ebenen die Grundprinzipien des Lean Managements verstehen. Das Bewusstsein für die Ziele und Vorteile der Lean-Methodik wird durch Schulungen und Workshops gefördert.
- Wertstromanalyse und Prozessoptimierung:
- Eine Wertstromanalyse hilft dabei, den aktuellen Zustand der Arbeitsabläufe zu verstehen und potenzielle Verschwendungen zu identifizieren. Auf Basis dieser Analyse werden Prozesse optimiert, um Effizienz zu steigern und Verschwendung zu minimieren.
- Einführung von Kanban und Pull-Systemen:
- Die Implementierung von Kanban und Pull-Systemen ermöglicht eine flexible und bedarfsorientierte Produktion. Diese Techniken unterstützen das Prinzip der Just-in-Time-Produktion und helfen, Überproduktion zu vermeiden.
- Kontinuierliche Verbesserung (Kaizen):
- Die Einführung einer Kultur der kontinuierlichen Verbesserung ist entscheidend für den langfristigen Erfolg von Lean Management. Teams sollten regelmäßig Verbesserungsmöglichkeiten identifizieren und umsetzen.
- Visuelles Management:
- Durch die Einführung von visuellem Management werden Informationen über den Status von Prozessen und Arbeitsabläufen transparent gemacht. Das erleichtert die Kommunikation und ermöglicht es Teams, schnell auf Veränderungen zu reagieren.
- Standardisierung:
- Die Entwicklung und Implementierung von Standardarbeitsweisen hilft dabei, Prozesse zu stabilisieren und Effizienz sicherzustellen. Standardisierung ermöglicht eine gleichbleibende Qualität und erleichtert die Ausbildung neuer Mitarbeiter.
- Führung und Unterstützung:
- Führungskräfte spielen eine entscheidende Rolle bei der Förderung und Aufrechterhaltung von Lean Management. Sie müssen die Veränderung vorleben, die Mitarbeiter unterstützen und die Ressourcen bereitstellen, die für eine erfolgreiche Implementierung erforderlich sind.
- Messung und Bewertung:
- Klare Leistungskennzahlen werden festgelegt, um den Fortschritt zu messen und den Erfolg der Lean-Initiative zu bewerten. Diese Metriken können die Effizienz, Qualität, Lieferzeit und Kundenzufriedenheit umfassen.
- Ausweitung auf andere Bereiche:
- Nachdem Lean Management erfolgreich in einem Bereich implementiert wurde, kann es auf andere Bereiche der Organisation ausgeweitet werden. Dies erfordert möglicherweise Anpassungen an die spezifischen Anforderungen verschiedener Abteilungen.
Die genaue Reihenfolge und Betonung dieser Phasen können je nach den individuellen Umständen einer Organisation variieren. Es ist wichtig, dass die Implementierung von Lean Management als kontinuierlicher Prozess betrachtet wird, der sich an die spezifischen Bedürfnisse und Gegebenheiten der Organisation anpasst.
Hier kommen Sie zu unseren Schulungsangeboten